L’optimisation logistique est au cœur de la stratégie de nombreuses entreprises. En effet, l’approvisionnement, le stockage, la préparation des commandes, l’expédition et le transport ont une influence directe sur la rentabilité d’une entreprise et sur la satisfaction client. Alors, pour optimiser leur chaîne logistique, les entreprises utilisent différentes techniques, dont la simulation.
En logistique, la simulation donne les moyens de déployer des améliorations sans risques. Mais comment l’utiliser concrètement ? En quoi la simulation répond-elle aux besoins d’anticipation d’une Supply Chain ? À quels niveaux intervient-elle et quelles situations peut-elle corriger ? Découvrez tous les avantages de la simulation pour optimiser une chaîne logistique.
L’optimisation logistique et la simulation pour apporter des solutions à des dysfonctionnements
Au sein d’une chaîne logistique, les dysfonctionnements sont très nombreux et peuvent avoir des répercussions sur la performance globale de l’entreprise. Il est donc primordial de savoir les détecter rapidement et d’y apporter une solution sur mesure.
Détecter les dysfonctionnements logistiques grâce à la simulation
Les anomalies d’une chaîne logistique sont aussi variées que ses activités. En effet, du stockage au transport, sans oublier le conditionnement ou la préparation des commandes, la chaîne logistique peut être perturbée par de nombreux incidents, comme :
- une hausse des coûts de stockage ;
- des retards dans la chaîne d’approvisionnement ;
- des pannes à répétition sur certains véhicules ;
- des collisions entre des chariots ;
- des intempéries ;
- des stocks mal gérés ;
- etc.
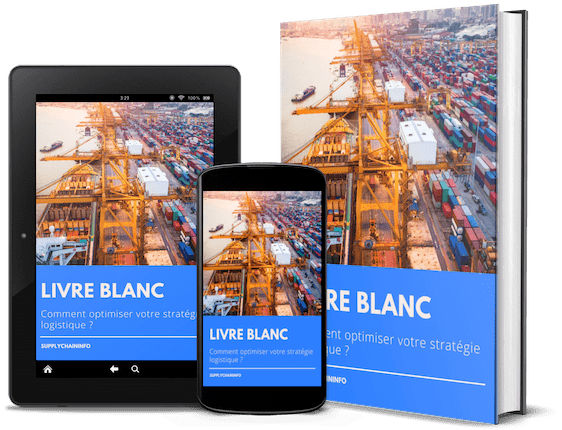
Comment optimiser votre stratégie logistique ?
Ponctuels ou répétitifs, ces incidents nuisent à la productivité et peuvent faire augmenter les coûts logistiques. Cependant, repérer l’origine d’un problème n’est pas chose aisée au sein d’une chaîne logistique. Flux physiques, flux d’informations ou flux financiers, il est nécessaire d’analyser un très grand nombre de données afin d’identifier un dysfonctionnement.
Faire le choix de la simulation, c’est opter pour l’efficacité. En effet, un système de simulation est en mesure d’identifier tous les risques ainsi que les variations de flux. De plus, il indique comment améliorer les performances de la Supply Chain et réaliser des économies de coûts.
La simulation pour mettre en place virtuellement des solutions dans la Supply Chain
Lorsque les dysfonctionnements ont été isolés au sein de la Supply Chain, il convient de les corriger. Mais apporter des systèmes correctifs au niveau du stockage peut entraîner des répercussions sur la chaîne d’approvisionnement. Alors, pour implémenter en toute sécurité de nouveaux processus, les entreprises s’appuient sur la simulation.
En effet, la simulation leur permet de créer une chaîne logistique virtuelle. Il s’agit d’une réplique exacte de la chaîne logistique réelle. Concrètement, cette simulation permet de tester virtuellement des solutions et d’analyser les répercussions sur l’ensemble des flux de la Supply Chain. Ainsi, les entreprises peuvent anticiper des changements de processus et utiliser efficacement l’ensemble de leurs ressources.
Utiliser la simulation dans l’optimisation logistique pour faire de l’anticipation
Tout au long de l’année, d’un mois à l’autre et d’une année à l’autre, les entreprises se projettent. Elles doivent faire face à des changements économiques et écologiques, mais également à des facteurs humains, qui peuvent impacter les performances de leurs activités logistiques.
Pourquoi l’anticipation est-elle nécessaire dans la gestion d’une chaîne logistique ?
L’anticipation optimise les performances d’une chaîne logistique. C’est un système qui permet de prendre en compte de très nombreux éléments, comme :
- les pics de saisonnalité et l’augmentation du nombre de commandes ;
- les restrictions de circulation ;
- l’augmentation du prix de l’énergie ;
- la gestion du personnel avec des absences, des congés, voire des arrêts maladie ;
- etc.
Tous ces éléments entraînent des répercussions directes sur les activités d’une chaîne logistique. De l’approvisionnement à la gestion de l’entrepôt, sans oublier la préparation des commandes, tout le personnel peut être impacté. Cependant, ces événements ne sont pas tous prévisibles.
Certes, les pics de saisonnalité peuvent être anticipés, car maîtrisés par l’entreprise. Mais l’augmentation du prix de l’énergie ou les absences imprévues du personnel sont des informations que les entreprises ne peuvent ni maîtriser ni anticiper. Pourtant, elles doivent être capables d’y faire face afin de conserver leur compétitivité et leur niveau de performance.
Comment la simulation répond-elle aux besoins d’anticipation d’une Supply Chain ?
La simulation est un outil performant pour réaliser des anticipations dans une Supply Chain. En effet, elle offre une représentation virtuelle de la chaîne logistique dans laquelle il est possible de faire des prévisions. Ainsi, l’entreprise est capable d’anticiper les moyens à mettre en œuvre. Elle peut faire face à toutes les situations, comme :
- l’absence de plusieurs salariés ;
- la mise en place de mesures restrictives concernant la circulation des véhicules ;
- la rupture de stock de plusieurs produits ;
- une panne d’électricité ;
- la défaillance d’un fournisseur ;
- l’arrêt de la chaîne de production ;
- etc.
Tous les cas de figure sont envisageables dans le cadre de l’optimisation logistique.
De même, si l’entreprise prévoit d’agrandir la surface de son entrepôt ou de faire l’acquisition d’un espace plus grand, elle peut également opter pour un modèle de simulation. Les données sont implémentées dans un logiciel qui analyse l’impact de chaque variable. Les responsables de la Supply Chain disposent ainsi de toutes les informations utiles pour prendre des décisions efficaces.
Le fonctionnement de la simulation pour l’optimisation logistique
Pour optimiser sa chaîne logistique, il convient de suivre quatre phases. En effet, le fonctionnement de la simulation logistique se base sur quatre étapes que nous vous présentons.
Étape n°1 : définition du besoin
La première étape consiste à déterminer l’objectif de la simulation. Ainsi, l’entreprise doit se demander ce qu’elle souhaite optimiser dans sa logistique :
- améliorer la satisfaction client ;
- réduire les coûts de transport ;
- diminuer les délais de livraison ;
- proposer aux clients de nouveaux modes de livraison ;
- réorganiser le stockage de certains produits ;
- augmenter la productivité ;
- faciliter des opérations de maintenance ;
- optimiser ses outils de gestion de stock ;
- etc.
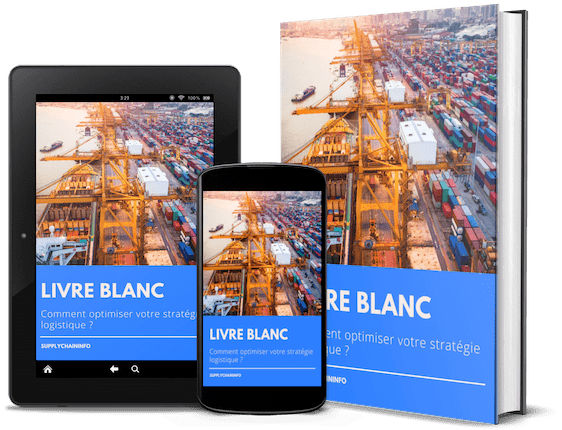
Comment optimiser votre stratégie logistique ?
Étape n°2 : collecte des données
Ensuite, lors de la deuxième étape, il est nécessaire de collecter les données. Une chaîne logistique, c’est un ensemble de flux de différentes natures :
- les flux physiques ;
- les flux monétaires ;
- les flux d’informations.
Les flux physiques concernent le déplacement d’un produit. En effet, de son site de production au client final, le produit circule sur un rayonnage, dans un entrepôt, dans un véhicule de transport, etc. Il peut également revenir à l’entrepôt dans le cas d’un retour colis. Toutes ces informations sont regroupées dans les flux physiques pour chaque produit.
Étape n°3 : développement du modèle
L’outil de simulation prend en charge l’analyse de l’ensemble des données logistiques afin de développer un modèle pertinent et adapté. Il s’agit de la troisième étape : la création d’un modèle. Ce modèle proposé par la simulation logistique permet de répondre à l’objectif principal de l’entreprise.
Étape n°4 : l’analyse des résultats et la mise en place des actions
Enfin, lors de la quatrième étape, l’entreprise analyse les résultats de la simulation. Elle peut ensuite les mettre en œuvre dans des solutions concrètes d’optimisation logistique. Grâce à ce mode de fonctionnement, les entreprises peuvent tester sans risque de nouveaux processus avant de les mettre en place au sein de leur entrepôt, de leurs rayonnages, etc.
En conclusion, la simulation intervient à tous les niveaux de l’optimisation logistique. Pour apporter des corrections à des processus logistiques déjà en place, anticiper l’avenir ou tester de nouvelles optimisations, la simulation est un des outils les plus fiables et les plus performants de l’optimisation logistique.
Nous vous recommandons ces autres pages :
- Comment utiliser la recherche opérationnelle pour l’optimisation logistique ?
- Quels sont les apports de la distribution directe dans l’optimisation logistique ?
- Comment gérer son réseau de distribution (network design) pour favoriser l’optimisation logistique ?
- Quelles sont les solutions de transport au service de l’optimisation logistique ?
- Comment utiliser l’approvisionnement centralisé dans l’optimisation logistique ?