L’optimisation des stocks est un levier majeur de compétitivité pour l’activité d’une entreprise. Elle lui permet de réduire ses coûts tout en se prémunissant face à une éventuelle rupture des produits. Découvrez les bons outils et méthodes pour parvenir à une gestion maîtrisée de votre entrepôt de stockage.
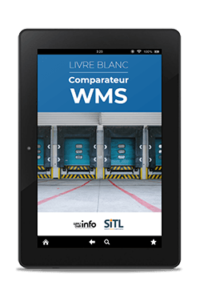
Améliorez votre gestion logistique en choisissant le logiciel WMS adapté à vos besoins !
L’essor du e-commerce, la rapidité des moyens de transport et des flux de communication oblige les entreprises à s’adapter : plus agiles, plus réactives et exigeantes, elles doivent faire face à une concurrence croissante pour satisfaire les besoins de leurs clients dans les meilleurs délais. Tout l’enjeu réside donc dans le choix des meilleurs fournisseurs, combinant qualité et rapidité de service. C’est pourquoi la gestion de l’entrepôt occupe désormais une place de premier ordre au sein de la supply chain. Bien au delà de son agencement, les méthodes adaptées pour l’entreposage, la gestion des stocks et le picking sont désormais au coeur des enjeux du supply chain manager. Une amélioration sensible de l’entrepôt permet directement de conquérir davantage de clients, et d’augmenter ses parts de marché.
Comment aménager efficacement votre entrepôt de stockage ?
Loin de n’être qu’une zone de stockage, l’entrepôt doit permettre aux équipes de manutention et de logistique de travailler efficacement. Elles assurent l’entreposage selon le type de marchandises à stocker sur palettes, racks, rayonnages et autres. L’organisation de l’entrepôt doit faciliter la préparation des commandes et l’acheminement des produits jusqu’au chargement pour livraison. Il prévoit également le passage des différents équipements de type chariot élévateur ou transstockeur pour palettes.
L’objectif numéro un de l’entrepôt de stockage est d’optimiser l’espace et les coûts de fonctionnement. Le système logistique en place doit cependant prendre en compte toutes les règles de protection et de sécurité du personnel. Après le processus de production, la méthode d’organisation s’adapte en fonction des flux de l’entrepôt.
Voici quelques solutions pour optimiser l’espace de stockage disponible :
- Avant de commencer votre activité, la réalisation d’un plan de mise en œuvre de l’entrepôt est essentielle. Il va permettre de répartir chaque zone en fonction des tâches et ressources correspondantes. N’hésitez pas à effectuer une simulation au sein de votre entrepôt pour vérifier la cohérence des flux de marchandises prévus.
- Avec pour but d’optimiser ces flux de marchandises et de personnes, il est important d’assurer une bonne circulation dans l’entrepôt. Les racks et rayonnages doivent permettre la bonne accessibilité des produits tout en réduisant au maximum le temps de préparation des commandes. Sur palette ou non, les stocks doivent être adaptés aux différents types d’engins de manutention jusqu’à la zone de chargement.
- Prévoir un espace pour le cross-docking contribue à faire gagner du temps à l’entreprise. Certaines marchandises peuvent ainsi être placées directement au niveau des quais de l’entrepôt sans passer par le stock. Ce système réduit les besoins en manutention et les délais de préparation des commandes.
- Lorsque la surface de stockage au sol du bâtiment est insuffisante, l’entreposage en hauteur est une solution idéale. Il permet d’augmenter la capacité de stockage de l’entrepôt tout en respectant les règles de sécurité. Il suffit de sélectionner un chariot élévateur adapté pour atteindre les marchandises en hauteur.
- Réduire la largeur des allées de rayonnages offre également une solution pour optimiser le stockage de l’entrepôt. Il convient néanmoins de s’assurer de l’espace restant pour un passage des engins de manutention en toute sécurité. Vous pouvez faire appel à l’automatisation de votre entrepôt avec des machines autonomes et des transstockeurs à palettes. Bien que coûteuses, elles représentent un gain de productivité considérable pour l’entreprise.
- Dans l’organisation de l’entrepôt, il convient de veiller à ranger vos produits en tenant compte de leurs spécificités. Certains produits comme les denrées alimentaires nécessitent un stockage particulier. Ils ne doivent pas se situer à proximité de produits Cela permet aussi de gagner du temps avec la manutention et la préparation des commandes de marchandises.
Quelles sont les règles à respecter pour parvenir à un stockage optimal ?
En matière de gestion d’entrepôt, la méthode ABC est certainement la plus répandue. Elle consiste à gérer vos stocks en attribuant une lettre à chaque produit en fonction de son importance. La lettre A est réservée aux produits contribuant le plus à votre chiffre d’affaires. La lettre B correspond à une deuxième catégorie de produits moins importants. Enfin, la lettre C est appliquée aux produits ne contribuant que marginalement à la réalisation de votre chiffre d’affaires.
Avec la méthode ABC, les produits étiquetés « A » ne doivent pas être en rupture de stock. Cela risquerait de pénaliser lourdement les performances de votre activité. Ils sont aussi ceux qui bénéficient d’un stock de sécurité pour prévenir les ruptures. Ils disposent d’un taux de service plus élevé que les autres produits. En limitant la quantité de stock pour les produits les moins prioritaires, ce système contribue à diminuer vos coûts.
L’optimisation des espaces de stockage constitue un autre levier de compétitivité. L’espace laissé entre chaque marchandise est important. Pour stocker vos archives, il n’est pas nécessaire d’en laisser. Cependant, l’extraction d’une marchandise de l’entrepôt nécessite de la saisir manuellement, ou à l’aide d’un outil adapté (robot automatisé, etc.) Pour de la manutention avec engin, laissez un jeu latéral de 75 mm et un jeu en hauteur de 100 mm. Autrement, vous perdrez un temps précieux à retirer chaque marchandise de l’entrepôt, ce qui diminue la productivité de vos salariés et de vos engins.
Faut-il adopter un système FIFO ou LIFO ? Il s’agit d’une question courante chez les supply chain managers. Dans le système FIFO, un côté du rayonnage sert à charger la marchandise, et l’autre est utilisé pour la prélever. Dans le système LIFO, le dernier produit entré est le premier sorti du stock.
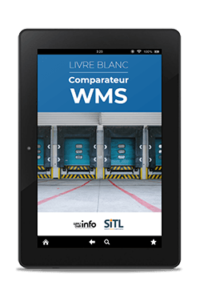
Améliorez votre gestion logistique en choisissant le logiciel WMS adapté à vos besoins !
L’optimisation de la gestion de votre entrepôt est une manne essentielle pour augmenter simplement la productivité de votre supply chain. La concurrence internationale diminue les marges de manœuvre des entreprises, et les oblige à réagir. Heureusement, l’application de quelques méthodes et outils simples permet immédiatement d’améliorer leurs performances.