La gestion de la logistique d’une entreprise est désormais un élément fondamental de son avantage concurrentiel : on bascule d’un modèle où la structure globale de toutes les sociétés s’affrontaient, vers un nouveau confrontant directement l’organisation et l’efficacité du système de production et de distribution.
Dans ce contexte, la gestion de la chaine logistique, ou supply chain management, devient un élément central, au cœur de toutes les préoccupations des chefs d’entreprises en 2019. Explications.
Qu’est-ce qui est susceptible d’optimiser vos coûts, vos délais, la productivité de vos salariés, la satisfaction de votre clientèle, vos relations fournisseurs, vos frais de transport et la profitabilité de votre société ? La réponse se situe immanquablement dans la gestion de votre logistique.
La logistique est une succession de processus internes comprenant de nombreuses étapes, du passage de la commande en passant par l’approvisionnement chez les fournisseurs et jusqu’à la livraison chez le client final. Il s’agit, étape par étape, d’estimer la juste valeur ajoutée à apporter au produit en fonction des attentes du client et de vos contraintes.
La chaîne logistique, aussi appelée supply chain, est également le principal levier de gestion de sa productivité sur le marché. Elle est au croisement entre les forces de ses fournisseurs, de ses clients, tout en observant les entrants potentiels et les produits de substitution. Impossible de ne pas la considérer comme la pièce maîtresse de sa compétitivité, dans un contexte d’ouverture des marchés et d’accroissement de la concurrence. Et pour cause, en 2019, améliorer sa stratégie logistique se place de nouveau parmi les préoccupations les plus importantes aux yeux des chefs d’entreprises.
Et pourtant, trop nombreux sont ceux qui regrettent de ne pouvoir compter sur une logistique véritablement à la hauteur des enjeux économiques et commerciaux de notre temps. Pour quelles raisons ? Comment y remédier ?
Découvrons ensemble tout ce qu’il faut savoir pour améliorer rapidement et efficacement la gestion de votre logistique pour votre société.
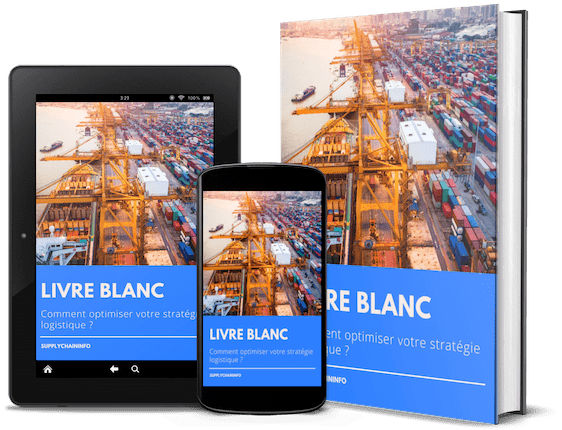
Comment optimiser votre stratégie logistique ?
I. Qu’est-ce que la gestion logistique ?
Une chaîne logistique complète gère non seulement tous les processus internes de l’entreprise, mais s’étend bien au-delà, avec la prise en charge de tous les flux entretenus avec son environnement.
Le supply chain management désigne un ensemble de théories et conseils pratiques destinés aux responsables de la chaîne logistique, afin d’en améliorer concrètement les performances. De nombreux ouvrages de théorie concentrent méthodes, moyens et ressources directement à votre disposition pour vous aider à mieux gérer et améliorer ses performances. A chaque étape, il convient d’améliorer l’agilité de votre structure, la rapidité des process et l’adéquation entre vos prestations et les attentes de votre clientèle. Bien que nous aborderons ultérieurement la question des KPI (Key Performance Indicator), le taux de satisfaction de votre clientèle est une boussole à ne jamais perdre de vue. Plus votre société est grande, plus les processus logistiques sont complexes, plus les méthodes sont sophistiquées et plus elles nécessitent une attention particulière. Une supply chain optimale combine donc rapidité, qualité et efficacité.
Améliorer sa fonction logistique résulte donc d’une démarche organisée, qui doit être accompagnée par le personnel de toute votre société et par vos prestataires logistiques. Il s’agit d’un vaste projet collectif méthodique pour une meilleure gestion des flux, et en particulier des flux transversaux. Cependant, de nombreux écueils doivent être connus : embourber votre entreprise dans des processus trop contraignants, pesants et coûteux est le risque principal dans lequel il est facile de tomber. Veillez à ne pas alourdir inutilement chaque étape, et sachez adapter le dispositif en fonction de vos besoins. Tout est donc question de méthode. Plus facile à dire qu’à faire ? Regardons ensemble de plus près comment y parvenir.
Les différentes étapes
Avant d’observer la manière dont il est possible d’améliorer la gestion de la chaîne logistique, commençons par en découvrir chaque étape :
- L’approvisionnement, constitue la sélection des meilleurs fournisseurs, articles et matières premières
- Le couple « fournisseur-matière première » désigne l’approvisionnement de l’entreprise en matières premières, dans le but de les transformer pour fabriquer des biens ou services.
- Le couple « client-produit » désigne le produit commandé par un client final, professionnel ou particulier
- La gestion de la clientèle
- La gestion des stocks et des entrepôts est au cœur de l’efficacité de votre supply chain
- Le transport des biens (transport de marchandises)
- La distribution des marchandises
- Le recyclage des marchandises, aussi appelé la « logistique inversée »
À terme, votre objectif est bel et bien d’améliorer la qualité du ou des services rendus à vos clients pour augmenter leur taux de satisfaction, et conquérir de nouvelles parts de marché.
II. Comment mesurer l’efficacité de votre chaîne logistique ?
Avant de vous lancer tous azimuts dans une campagne d’amélioration de votre supply chain, encore faut-il savoir où concentrer vos efforts. Réalisez un audit interne de chaque étape et réalisez des tableaux de bord logistique afin de mieux connaître les points précis auxquels il serait préférable d’apporter des corrections.
A. Comment améliorer la satisfaction de vos clients ?
La satisfaction de votre clientèle doit demeurer votre première priorité. C’est la qualité de votre réponse apportée pour répondre aux attentes qui détermine cette satisfaction. Pour la mesurer, soyez attentif au taux de service. Il s’agit d’un indicateur permettant de mesurer l’efficacité globale de la chaîne de fabrication. C’est un KPI fondamental pour l’évaluation de vos performances. Vous pourrez ainsi connaître la quantité d’articles livrés conformément aux conditions prévues dans votre contrat de vente (conformité de la nature et de la qualité du produit, délais de livraison, etc.)
Le taux de service est donc élevé lorsque vos commandes sont livrées dans les temps, lorsque la nature et la qualité des articles coïncide avec les attentes de votre clientèle. Il s’agit donc de déterminer la quantité de chaque produit à détenir en stock (nous reviendrons plus précisément sur cet aspect ultérieurement), afin de vous prémunir contre les éventuelles ruptures. Plus une rupture de stock est coûteuse (allongement des délais de livraison, et possible perte de clients à court et moyen terme), plus il faut augmenter votre quantité de biens stockés, et vice-versa.
Il faut calculer le taux de service sur la durée d’un exercice afin d’être véritablement représentatif. Pour mesurer le respect des délais, divisez le nombre de commandes livrées dans les temps par la quantité totale de commandes. Plus mesurer la qualité du ou des services, divisez le nombre de litiges sur commandes diminués du nombre de commandes livrées hors délais par la quantité totale de commandes. Veillez donc à bien pondérer chaque critère, afin d’obtenir des résultats fiables.
Pour améliorer votre taux de service
Vous pouvez attribuer une lettre à chaque produit en fonction de son degré de priorité dans la réalisation de votre chiffre d’affaires :
- « A » pour les 20% des articles les plus importants, on parle de produits critiques.
- « B », pour les 25% suivants, on parle de produits intermédiaires.
- « C » pour les 50% restants, on parle de produits secondaires.
Autrement, il est possible de comparer directement les coûts générés par le stockage avec celui d’une rupture de stock. Il est difficile d’évaluer réellement les conséquences et pertes générées par une rupture, notamment à moyen terme. Autant que possible, il convient donc de chercher à améliorer le taux de service des biens de catégorie A, ou ceux dont le coût d’une rupture de stock est très élevé.
À l’inverse, il est également stratégique d’étudier le taux de rupture qui mesure la capacité d’une entreprise à disposer des marchandises en stock. Les ruptures de stock ont des conséquences directes sur la satisfaction de votre clientèle, c’est pourquoi il est primordial de les éviter au maximum. Une personne qui ne trouve pas le produit dans votre entreprise pourra vite partir chez votre concurrent, et in fine ceci pourrait avoir des conséquences directes sur la compétitivité de votre entreprise.
Pour calculer ce KPI, vous pouvez utiliser cette formule : Nombre de commandes non honorées dues à des ruptures de stock / Quantité totale de commandes.
Le calcul de ce ration peut se faire en fonction de vos différentes marchandises pour une meilleure vision de la proportion de vos stocks.
B. Comment optimiser la gestion de vos stocks ?
À chaque étape son propre KPI. Il en existe pour évaluer l’efficacité de toute votre logistique. La gestion de vos stocks est un élément clé pour la réduction des frais logistiques. En effet, il faut non seulement disposer d’un entrepôt, mais aussi de toutes les machines-outils et infrastructures indispensables pour le faire fonctionner. Plus l’entrepôt est vaste, plus les équipements sont importants, et plus vos dépenses d’investissement et de fonctionnement seront élevées. Il ne s’agit donc pas de diminuer à tous prix le niveau des stockages, mais de le rendre le plus proche possible de vos besoins.
La question de l’approvisionnement est donc centrale. La formule de Wilson est une solution efficace pour utiliser au mieux vos capacités, en limitant les coûts de commande. Aussi connue sous le nom de quantité économique de commande (QEC), la formule de Wilson détermine la quantité optimale de l’approvisionnement d’une unité de production. L’équilibre optimal est atteint lorsque une commande est passée de manière à réduire le coût de possession des stockages, en évitant la pénurie. Seuls 3 paramètres doivent être pris en compte pour y parvenir : la demande en quantité sur la période (D), le coût d’une commande incluant le transport et la réception de la marchandise (CC), et le coût unitaire de possession du stock (CS).
La formule suivante donne la quantité optimale à commander :
La formule de Wilson s’applique principalement lorsqu’il s’agit de commandes régulières et de quantités identiques. Aussi, la variation du prix de l’approvisionnement n’est pas prise en compte. Parfois, les réapprovisionnements sont anticipés en prévision d’une augmentation du prix des articles.
Autre KPI à déterminer, le stock de sécurité (ou « stock tampon »). Ce KPI correspond à la quantité minimale d’un produit nécessaire pour optimiser vos frais de stockage tout en limitant le risque de rupture de stock. Il est important qu’elle ne tombe pas en dessous de ce niveau pour ne pas faire courir de risque au bon fonctionnement de la chaîne de fabrication. Celui-ci est particulièrement utile en cette période de volatilité des marchés, durant laquelle les firmes ont besoin d’être toujours plus agiles. Il permet donc de limiter les ruptures de stock dues aux aléas. Tous les articles ne sont pas soumis à la même volatilité, c’est pourquoi il est préférable de répliquer le système de classement ABC, que nous avons précédemment exposé. Le coefficient de sécurité est déterminé par la loi normale et dépend de votre taux de service choisi.
Par exemple, pour un taux de 99%, le coefficient de sécurité est égal à 2,326. Pour un taux de service de 98%, le coefficient de sécurité est égal à 2,05. Pour savoir à quel montant commander de nouveau, il suffit de connaître le seuil à partir duquel vous souhaitez être réapprovisionné. Le point de commande est obtenu en multipliant la demande moyenne par période par le délai de réapprovisionnement auxquels on ajoute le stock de sécurité.
C. Quels sont les autres KPI à vérifier ?
Autre point important, le calcul du prix de transport de vos marchandises. Vous pouvez opter pour une taxe au poids. Elle dépend du poids réel évalué à la tonne et du volume en mètres cubes occupé par vos articles. Ces deux paramètres permettent d’établir le poids taxable de vos articles. Autrement, il est possible de préférer le paiement d’une taxe forfaitaire, calculée pour un container par exemple. Cela dépend du poids de vos articles et de leur volume.
Enfin, voici une liste d’autres KPI logistique et d’indicateurs de production à inspecter avec attention :
- La capacité de fabrication inutilisée se calcule en retranchant le volume standard disponible par le volume réel produit dans la période.
- Le coût d’arrêt par équipement se calcule en additionnant le total des coûts générés par l’arrêt d’un ou plusieurs équipements. Parfois, ils augmentent lorsque plusieurs équipements sont à l’arrêt en même temps. Il est aussi intéressant d’observer la durée moyenne des arrêts.
- Le coût de revient par produit désigne la somme des coûts liés au cycle de fabrication. Il permet de déduire votre marge brute
- La densité des files d’attentes (en %) s’obtient par la formule suivante : (Volume de fabrication en cours / Total réalisé)*100
- La durée moyenne du cycle de fabrication s’obtient par la forme suivante : Somme des durées du cycle de fabrication/ nombre d’ordres planifiés
- L’emploi des équipements (en %) s’obtient par la formule : (Temps total réel de fabrication / Temps total théorique de fabrication)*100
- La fluidité de la fabrication (en %) s’obtient par la formule : (Volume de fabrication réalisé dans les temps / total de fabrication de la période)*100
- Le taux de pertes (en %) s’obtient par la formule : (Quantité ou valeur des pertes de production / Quantité ou valeur produite)*100
III. Comment optimiser la gestion de vos stocks ?
Plusieurs méthodes permettent concrètement d’améliorer la gestion de vos stocks, et, en premier lieu, le DDMRP permettant d’instaurer une gestion dynamique de « buffers » (stock tampon). La gestion logistique est entièrement pilotée par la demande, et les buffets sont totalement inclus dans la gestion des flux de production. En introduisant des stocks tampons à des points stratégiques, vous garantissez une excellente réactivité à votre organisation, et gardez toujours un œil attentif sur la demande. Cette méthode permet d’atténuer les variations du marché entre 20% et 30%. Les sociétés soumises à une forte volatilité, dont les délais d’approvisionnement sont importants et dont les process d’assemblage complexes ont tout intérêt à appliquer cette méthode.
Le flux tiré
La production à « flux tiré » consiste à placer le client comme générateur des ordres de production. Il émet une demande, et l’entreprise fournit le produit désiré. Cela limite le stock, et peut même le supprimer totalement dans certains cas. D’autres articles nécessitent un délai de fabrication trop long et ne peuvent être soumis à cette pratique (les voitures ou les marchandises agricoles par exemple). Pour cette raison, il est possible d’appliquer un ou plusieurs stockages intermédiaires tout au long de la chaîne de fabrication. Ce type de management est très efficace pour optimiser la gestion et le niveau du stockage.
Le flux poussé
À contrario, le « flux poussé » se fonde sur les prévisions de la demande pour organiser la fabrication. Le produit est fabriqué avant que le client n’ait effectué son ordre de commande. L’entreprise n’a pas la certitude de vendre ses articles, et constitue des stocks. Cette méthode permet au client d’être livré très rapidement après le passage de la commande. Ce type de management est donc efficace dans certains cas, lorsque la clientèle attend à recevoir leur commande rapidement.
Enfin, le cross docking est une méthode qui connaît un essor important en France et à l’international, et particulièrement chez les commerçants, distributeurs, grossistes et centres de distribution qui ne possèdent pas de stock. Concrètement, vous faites passer de la marchandise de la plateforme de déchargement vers le quai d’expédition sans passer par l’entrepôt de stockage. Les articles ne font donc que transiter. Exit la préparation de la commande, la réexpédition, le picking et le colisage. Rapidité de traitement et réduction des coûts font partie des avantages attendus de cette méthode. Ce système est largement appliqué dans la grande distribution ou pour les livreurs de la presse quotidienne par exemple.
IV. Quelles sont les autres bonnes méthodes et pratiques à adopter ?
Commençons par nous intéresser au picking logistique. Il s’agit d’une étape incontournable, et trop souvent négligée. Elle désigne le moment durant lequel un produit est prélevé dans le stock, puis rassemblé avant son expédition dans une commande. L’organisation des articles dans les entrepôts est donc essentielle. Elle doit obéir à une stricte cohérence, avec une référence précise pour chaque produit. Certains logiciels WMS (Warehouse Management System) permettent d’optimiser le picking en choisissant le meilleur chemin à réaliser pour prélever chaque produit et ne pas revenir plusieurs fois au même endroit. La gestion de plusieurs commandes en même temps doit également s’appuyer sur une solution de transmission performante de l’information. Suivre la préparation des commandes est possible grâce à des terminaux informatiques embarqués dotés d’un système de codes-à-barres.
Les logiciels WMS permettent d’améliorer le fonctionnement de tout votre entrepôt de stockage. En effet, il doit non seulement permettre de stocker des biens de la meilleure manière possible, d’opérer aisément dans cet espace et de réaliser les opérations d’inventaire. Certains articles nécessitent une attention spécifique. Aussi, une bonne gestion des entrepôts passe par la gestion des ressources humaines, la division du travail, la spécialisation des travailleurs et le classement des articles par ordre de priorité. Chaque produit doit posséder une zone particulière et doit, si possible, transiter via le cross docking sans passer par votre entrepôt logistique. Enfin, assurez un contrôle qualité sur le long terme en mesurant régulièrement vos performances.
La logistique e-commerce est au cœur de toutes les attentions, et concentre de nombreux enjeux qui lui sont propres. La concurrence sur le marché oblige les sociétés à toujours garantir la disponibilité des articles tout en optimisant les coûts de stockage. Aux yeux des clients, les frais de port occupent une dimension symbolique très importante. Un tarif inférieur à 5€, ou 10€ pour un article volumineux est recommandé. Au-delà, il constitue un frein conséquent. Enfin, veillez à offrir une gamme de modes de livraison à des tarifs et délais variés, pour s’adapter aux besoins de votre clients. Enfin, votre politique de retour doit être souple et bien organisée pour susciter leur confiance. De plus en plus d’acteurs du e-commerce décident d’externaliser certaines tâches à faible valeur ajoutée.
Pour conclure
La chaîne logistique cristallise aujourd’hui les préoccupations de nombreux chefs d’entreprises en raison de l’enjeu stratégique qu’elle représente pour la croissance de l’entreprise. Les nombreux exemples pratiques cités au cours de cet article suffisent à le prouver : une bonne gestion de votre supply chain est un avantage concurrentiel déterminant pour accroître vos parts de marché et maintenir la pérennité de votre société. Des progrès visibles et significatifs peuvent être réalisés en très peu de temps, à condition d’apporter les méthodes et outils adéquats. Pour aller plus loin, n’hésitez pas à consulter notre guide, pour avoir un aperçu de l’ensemble des solutions.
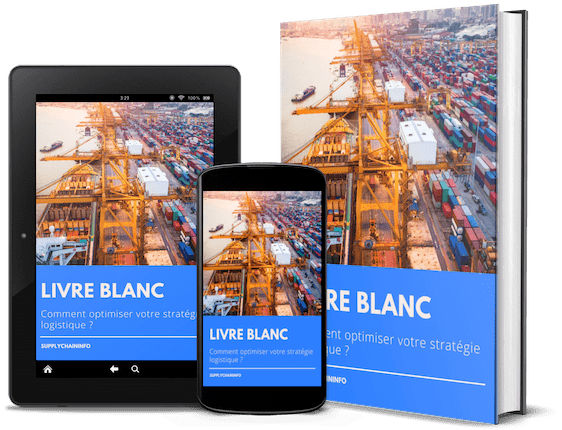
Comment optimiser votre stratégie logistique ?